How to Choose the Best Attendance Software for Chemical Manufacturing
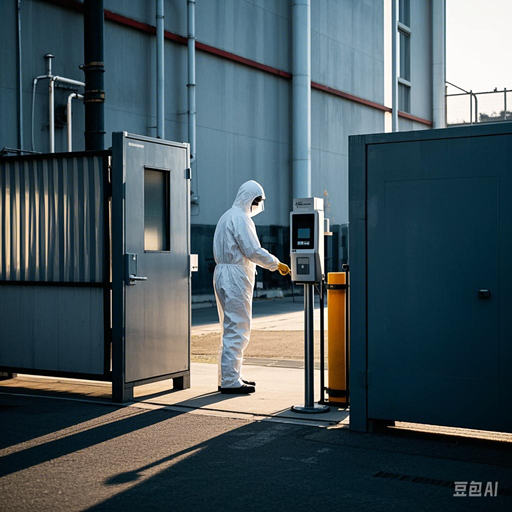
An efficient attendance system is vital for chemical manufacturing companies. It helps track employee hours, monitor productivity, and ensure safety compliance—three critical factors in an industry where precision and accountability are non-negotiable. However, with so many attendance software options available, how do you determine which one best meets your company's unique needs?
In this guide, we’ll explore the specific challenges of the chemical manufacturing industry, the must-have features for attendance software, and the pros and cons of different system types. By the end, you’ll have a clear roadmap to help you select the best attendance software for your operations.
The Challenges of Attendance Tracking in Chemical Manufacturing
Chemical manufacturing presents unique challenges that demand specialized attendance solutions. These challenges include:
- Hazardous Materials: Employees working with dangerous chemicals need to be tracked meticulously. Knowing who accessed specific materials and when is critical for safety and compliance.
- Shift Work: With multiple shifts across the day and night, systems must be flexible to handle varying schedules.
- PPE and Coveralls: Employees often wear bulky protective gear like gloves, goggles, or respirators, which can interfere with traditional badge scanning or biometric systems.
- Remote Locations: Many facilities are spread across large campuses or remote sites, making centralized attendance tracking harder to implement.
Key Features to Look for in Attendance Software
When choosing attendance software for your chemical manufacturing operation, prioritize the following features:
1. Detailed Tracking
The software should accurately log clock-in/out times, break durations, department transfers, and specific location data. This level of detail helps monitor shift adherence, track time spent on hazardous tasks, and ensure compliance with safety regulations.
2. Flexibility
Your software must adapt to various shift patterns, job roles, and pay policies. It should accommodate early or late clock-ins and adjust to the specific requirements of different departments.
3. Notifications and Alerts
Real-time alerts can signal when an employee misses a clock-in, leaves early, or fails to clock out. These notifications allow managers to respond quickly to potential emergencies or staffing issues.
4. Access Control Integration
Attendance software that integrates with access control systems ensures that employees can only enter restricted areas if they are properly clocked in. This adds an extra layer of safety and compliance.
5. Robust Reporting
Detailed, customizable reports can provide insights into hours worked, absenteeism trends, overtime, and productivity. These reports help managers make informed decisions and maintain compliance with labor laws.
6. Durability
In chemical plants, hardware like clock-in terminals must be durable enough to withstand extreme conditions, including moisture, dust, and chemical exposure. Look for rugged designs that can handle these environments.
Comparing Attendance System Types
Let’s examine the most common types of attendance systems and their suitability for chemical manufacturing:
1. Biometric Systems
- Pros: High accuracy, prevents buddy punching, works well with PPE.
- Cons: Higher cost, potential concerns about privacy.
2. Proximity Card Systems
- Pros: Quick and contactless, easy to replace cards, affordable.
- Cons: Cards can be lost, damaged, or shared (buddy punching).
3. Barcode Badge Systems
- Pros: Low-cost badges, can track specific activities.
- Cons: Barcodes can be damaged, slower clock-in process.
4. Web & Mobile Apps
- Pros: Convenient, real-time alerts, integrates with payroll systems.
- Cons: Requires reliable internet, may not suit all employees.
Key Considerations by Role
When deciding on attendance software, different roles in your organization will have unique priorities. Here’s what to focus on:
- Operations Managers: Job costing, labor tracking, and absenteeism reports.
- HR Managers: Payroll integration, customizable pay policies, compliance reporting.
- Safety Managers: Restricted access, hazardous material tracking, emergency roll-call features.
- IT Managers: Cybersecurity protections, disaster recovery, technical support.
How to Implement Your New Attendance Software
Selecting the right attendance software is only half the battle. To ensure a smooth rollout, follow these best practices:
- Involve Employees Early: Gather feedback and build support.
- Start with a Pilot Program: Test the software in one department or location first.
- Provide Thorough Training: Ensure all users understand how to use the system.
- Communicate Frequently: Share updates and address questions promptly.
- Monitor and Optimize: Review early data and make adjustments as needed.
Key Takeaways
Choosing the right attendance software for chemical manufacturing requires careful consideration. Remember to:
- Prioritize detailed tracking, flexibility, alerts, and access control integration.
- Compare biometric, proximity card, barcode, and mobile app-based systems.
- Involve key stakeholders like operations, HR, safety, and IT teams.
- Roll out the system gradually with proper training and communication.
By following these steps, you can implement an attendance system that enhances productivity, ensures safety, and meets your organization's unique needs.